圖7 A-A方向料頭流速分布和變形圖(向左邊彎曲,且幅度較大)
圖8 從A-A視圖方向看過去的料頭(向左邊彎曲,且幅度較大)
(5)型材流速和實(shí)際變形分析對照:

圖9 B-B 料頭流速分布和變形圖 (向左邊稍微彎曲)
圖10試模結(jié)果,C-C視圖顯示,從C-C方向看過去,型材向右邊彎曲;
(1)型材速度和變形模擬分析:整體流速不平衡,相差較大,圖3顯示, 型材左側(cè)的流速慢,右側(cè)流速較快 ,最快速度為圖3中 。且最快與最慢兩者相差177.3 mm/s,所以料頭向左側(cè)彎曲。
圖9模擬結(jié)果,B-B視圖顯示,從B-B方向看過去,型材向左邊彎曲;
C-C 視圖和B-B視圖方向剛好相反,顯示的彎曲方向也相反。表明模擬結(jié)果和試模結(jié)果是一致的。
圖9 B-B 料頭流速分布和變形圖 (向左邊稍微彎曲)
圖10 從C-C 視圖方向看過去的料頭(向右邊稍微彎曲)
3.2 根據(jù)模擬結(jié)果進(jìn)行優(yōu)化設(shè)計(jì)
根據(jù)以上結(jié)果進(jìn)行綜合分析結(jié)果對初始設(shè)計(jì)方案進(jìn)行修改。對二級導(dǎo)流(二級導(dǎo)流二維圖如下圖11所示)進(jìn)行優(yōu)化修改,如下圖12所示:
圖11 模具二級二維圖
圖12 優(yōu)化設(shè)計(jì)示意圖
3.3 優(yōu)化結(jié)果分析
根據(jù)優(yōu)化好的設(shè)計(jì)加工模具,并上機(jī)試模,通過跟蹤發(fā)現(xiàn),根據(jù)后續(xù)跟進(jìn),優(yōu)化后模具生產(chǎn)出的型材得到優(yōu)化,料頭較為平整。
從實(shí)際生產(chǎn)中可以找到很多型材,未優(yōu)化的時,大多出現(xiàn)料頭不平,單孔中快慢相差大、多孔出料速度差距較大等缺陷,如圖13所示。由此可見使用有限元軟件進(jìn)行優(yōu)化設(shè)計(jì)是有有必要的。
圖13 未經(jīng)優(yōu)化產(chǎn)出的料頭
4 結(jié)論
(1)利用HyperXtrude平臺能夠有效地對擠壓過程進(jìn)行仿真模擬,可節(jié)省大量設(shè)計(jì)時間,模擬結(jié)果對實(shí)際生產(chǎn)具有很高的參考價值。
(2)運(yùn)用有限元分析軟件對擠壓過程進(jìn)行模擬,可有效減少試模次數(shù),發(fā)現(xiàn)憑借經(jīng)驗(yàn)難以發(fā)現(xiàn)的結(jié)構(gòu)缺陷,從而降低企業(yè)成本,提高型材質(zhì)量。
參考文獻(xiàn)
[1] 宋杰. 薄壁鋁型材擠壓過程仿真及模具優(yōu)化設(shè)計(jì)[D]. 湖南省長沙市.中南大學(xué).2006.
[2] 李積彬,伍曉宇,劉科勝.鋁型材擠壓模具的3D優(yōu)化設(shè)計(jì)[J],機(jī)械設(shè)計(jì),2000,6(6):29-32.
[3] 盛偉,謝配良,陳勝. ANSYS二次開發(fā)軟件在塑性成形模擬中的應(yīng)用[J]. 機(jī)車車輛工藝,2002(6):24-27.
[4] 于滬平,彭穎紅,阮雪愉. 平面分流焊合模成形過程的數(shù)值模擬[J]. 鍛壓技術(shù),1999年,24(5): 9-11.
[5] 劉漢武,丁樺,崔建忠. 鋁型材擠壓分流組合模有限元分析與計(jì)算[J]. 模具工業(yè),1999年,(4): 9-11.
上一頁12下一頁
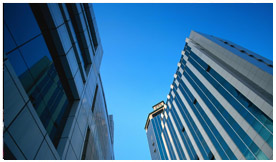
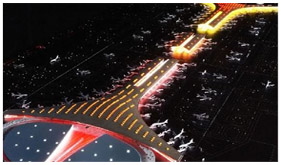
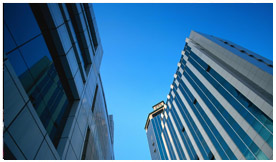
[摘 要]點(diǎn)支承開孔玻璃板承受垂直于板面的均布荷載時,開孔周圍分布著較大的集中應(yīng)力,顯著影響著玻璃板的承載性能。目前國內(nèi)外對于點(diǎn)支承單層玻璃板孔邊應(yīng)力的研究較多,但關(guān)于中空玻璃板孔邊應(yīng)力的研究尚不多見。本文利用有限元方法求解四點(diǎn)支承中空